製造業か抱える経営課題とは?人材や技術継承など多面的に解説
2023年6月28日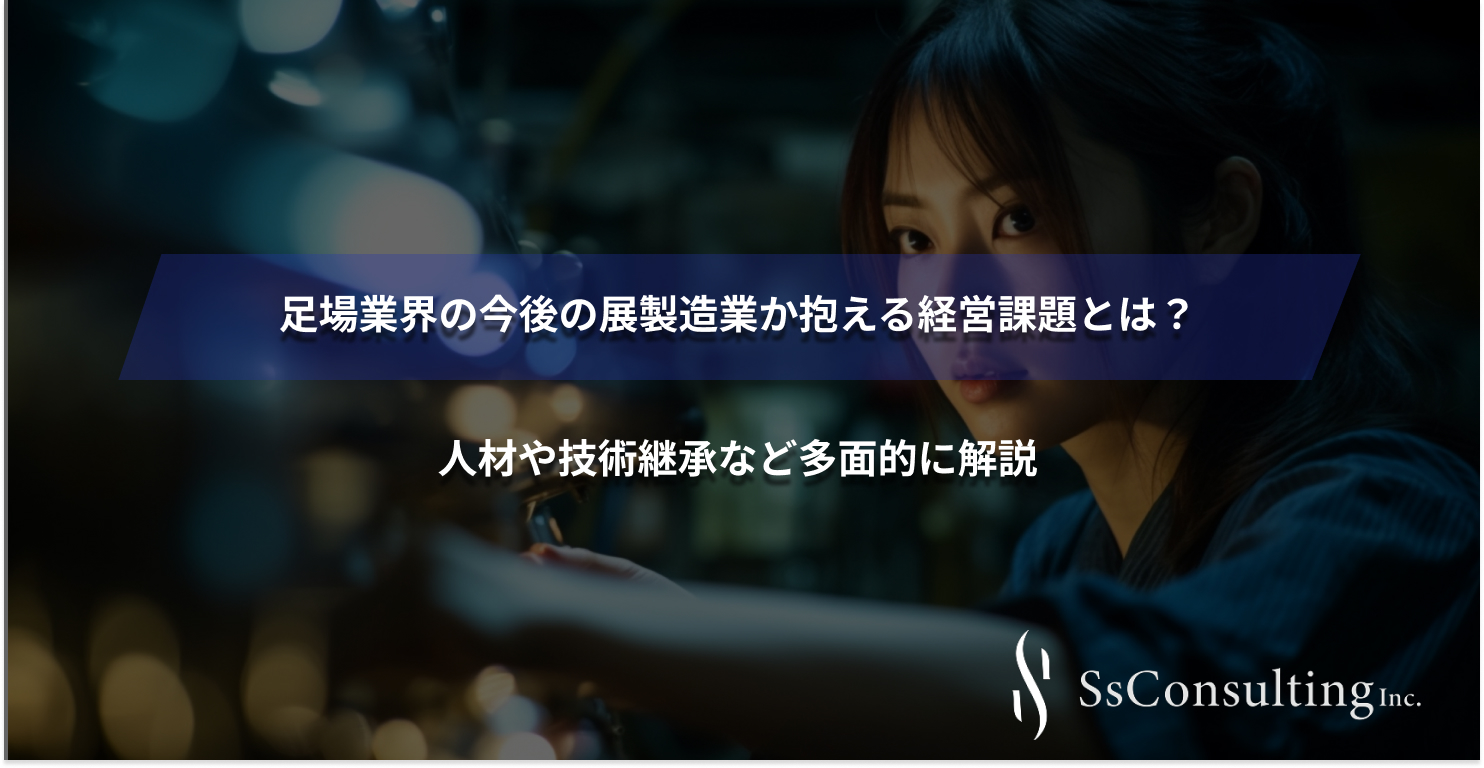
製造業は我が国を支える基幹事業ですが、経営者の高齢化や人材不足や人材育成など様々な課題を抱えている企業が多いです。
特に地方の中小企業に多く、何が課題なのかもつかみ切れていないケースも多く存在します。
本記事では、そんな製造業者が抱える経営課題の解決方法について詳しく解説し、弊社事例も紹介します。
経営が上手くいかない、なぜか売上が上がらないという方は参考にしてみてみてください。
製造業が抱える経営課題
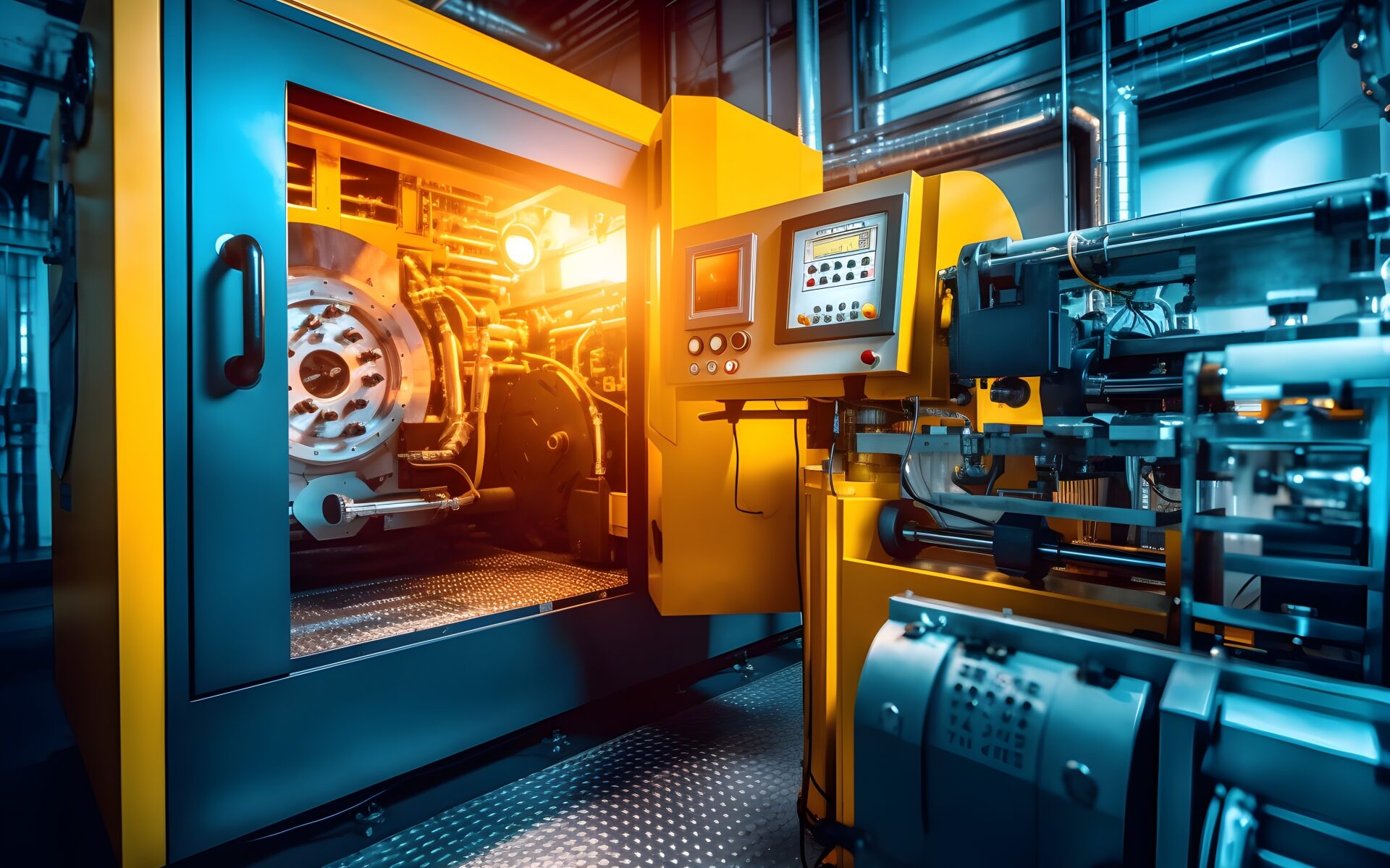
製造業は資金面や材料調達先の調整など、経営において様々な課題を常に抱えています。
よりコストを抑え、円滑に経営をするための企業努力が必要です。
その上で、具体的な経営課題として現代では以下のようなことが挙げられます。
- 人材不足
- 後継者問題
- 技術継承の課題
- DX推進の遅れ
- 若手人材の育成が進まない
経営課題を解決することにより、販路拡大や売上向上に繋がるため参考にしてみてみてください。
人材不足
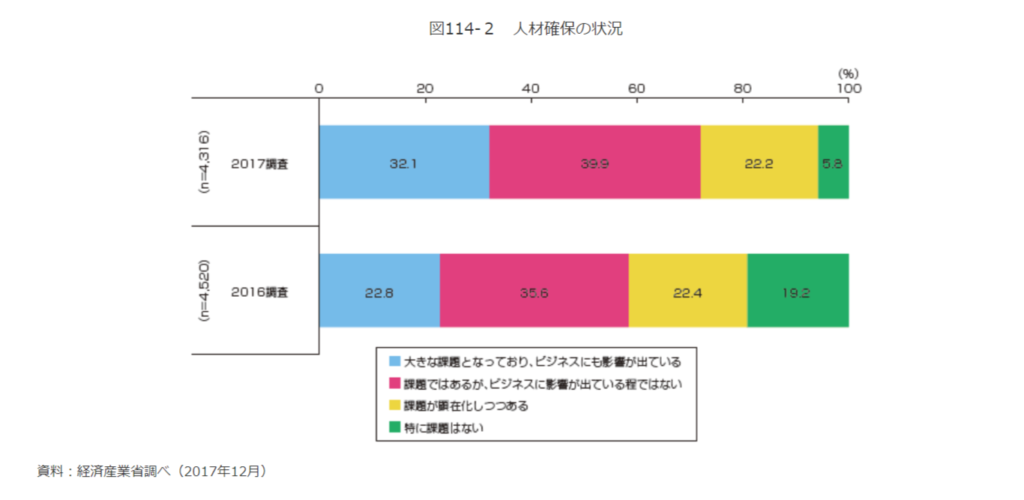
引用:経済産業省
人材不足は、製造業において深刻な問題とされていて2017年の調査では「大きな課題となっており、ビジネスにも影響が出ている」と回答した割合が約32%でした。
ただ、人が少ないだけではなく製造業で働く人材の高齢化も深刻化しているといわれています。
そのため、ただ人数が増えればよいのではなく、若く会社を担えるような若手人材が増えなければいけません。
一方で、地方の製造業では求人条件が時代にあっておらず、若手が入りにくいという明確な原因があることも多いです。
課題解決のために、求人条件が若手が働きたいと思えるような内容なのかも確認してみてみましょう。
後継者問題
製造業で、経営者の手腕で会社が成り立っているケースがあり、経営者の人脈や取り引き先との関係性で売上を維持しているケースは少なくありません。
しかし、経営者が年齢や病気などでリタイアしてしまったら、その先の経営は不安定になります。
そのため、後継者を育成するか外部からの採用が必要です。
人材を採用するほかに、M&Aを行い事業承継することもひとつの手です。
事業承継をする場合、M&A業者やコンサルタントの手助けが必要なのでプロの手を借りましょう。
技術継承の課題
製造業において、技術は会社にとって命であって売上をつくる上で基幹となる要素です。
手の感覚が商品の精度に影響が出る場合、技術継承は必要不可欠になります。
しかし、古い会社ほど技術がマニュアル化されておらず、人から人へ感覚の世界で伝達されていることが多いです。
若手人材は、この感覚で覚えることが苦手である傾向があり、技術が定着せずに教え方に不満を持ち会社を去っていきます。
そのため、より後ろの世代に技術を伝えるためにも、技術継承をスムーズにする方法を模索することが必要です。
DX推進の遅れ
DXは、デジタルトランスフォーメーションの略でアナログで行っていたことをデジタル技術を活用し、業務効率化を目指すことを指します。
具体的には、帳簿や各種書類などを紙からデジタルに変える、製造チェックをIT機器に変えるなどが挙げられます。
DX推進は製造業で遅れているとされ、業務効率化が進まないことから想像数を増やせずに時代に取り残されてしまう可能性があるのです。
障壁として、在籍している従業員がIT機器の扱いになれていないことから、導入しても難しいのではないかという考えが多く見られます。
実際、導入をしてみるといままでより業務が楽になるほか、労働時間の大幅な削減にもつながるので検討してみてみてください。
若手人材の育成が進まない
高齢化が進んでいる製造業の現場において、若手人材は貴重です。
しかし、「見て覚える」「マニュアルはない」などの古い教育体制で、若手人材が育たないケースがあります。
また、技術があり優秀であるのに年功序列が根付いて、昇進するまで何年もかかるなども育成が進まないケースになります。
若手育成をマニュアル化して、定着できるような仕組みをつくることが経営課題解決のヒントになるでしょう。
製造業が存続のために取り組むべき対策
製造業が経営課題を解決し、企業を存続させるために取り組むべき対策は以下のようなことが挙げられます。
- ICT導入
- 技術のマニュアル化
- 無駄な経費の削減
いきなりすべて導入することは難しいですが、徐々にでも進めていくことで改善につなげられます。
ICT導入
ICT導入のICTとは、「Information and Communication Technology」の略で日本語で情報通信技術と訳されます。
ICT導入は具体的に何をするかというと、スケジュールや勤怠、資料などをデジタル化するためにPCやタブレットを導入することを指します。
従来、紙で勤怠を打刻していて入力するのに時間がかかっていたケースが、ICT導入によって明確に従業員の勤務状態を見られるようになるなどあげられます。
しかし、従来のやり方に慣れている従業員にいきなり変えてしまうと、反発がある可能性があります。
そのため、ICT導入のために機器の説明や難しくないことを理解してもらうためのディスカッションから始めましょう。
技術のマニュアル化
技術が浸透しないと、新しい人が入ってきても戦力になるまでに時間がかかります。
従来の人ができていても、若い人には教え方が正しくない可能性があるのでマニュアル化は必要不可欠な工程です。
また、外国人の労働者も採用できるように文字だけではなく、絵でもわかるように工夫が必要です。
細かいコツなどは、人の手で教える必要がありますが、業務工程など伝えなくてもわかる範囲はマニュアル化しておきましょう。
マニュアル作成が難しい場合、第三者を頼り作ってもらうこともひとつの手です。
無駄な経費の削減
経営において経費の活用は必要であり、必要経費のためであれば利益余剰金を投入することは悪いことではありません。
しかし、必要以上の接待交際費や福利厚生費によって会社の経営を圧迫している場合、調整する必要があります。
会社の私物化にも思われ、従業員からの反感を買ってしまう可能性があるため、無駄な経費は削減して従業員に還元できるようにしましょう。
また、資金が残っていれば求人を出せたり、新たな人材を雇うこともできます。
経営課題解決につながるスマートファクトリー
スマートファクトリーは、AIやIoT技術を駆使してデジタルデータを使って工場を管理する仕組みを指します。
IoT技術のIoTとは、「モノとインターネット」の意味があり、従来オンラインで接続されていなかったモノをインターネットに繋ぎより便利にする技術です。
ロボットを使って自動化する意味ではなく、あくまで工場の生産性をITの力で引き上げる意味合いがあります。
経営課題を抱えている製造業者の場合、スマートファクトリー化することによって改善されるケースがあります。
導入は自社で全て行う必要はなく、スマートファクトリー化を支援している企業があるため相談してみましょう。
工場をスマートファクトリー化する利点
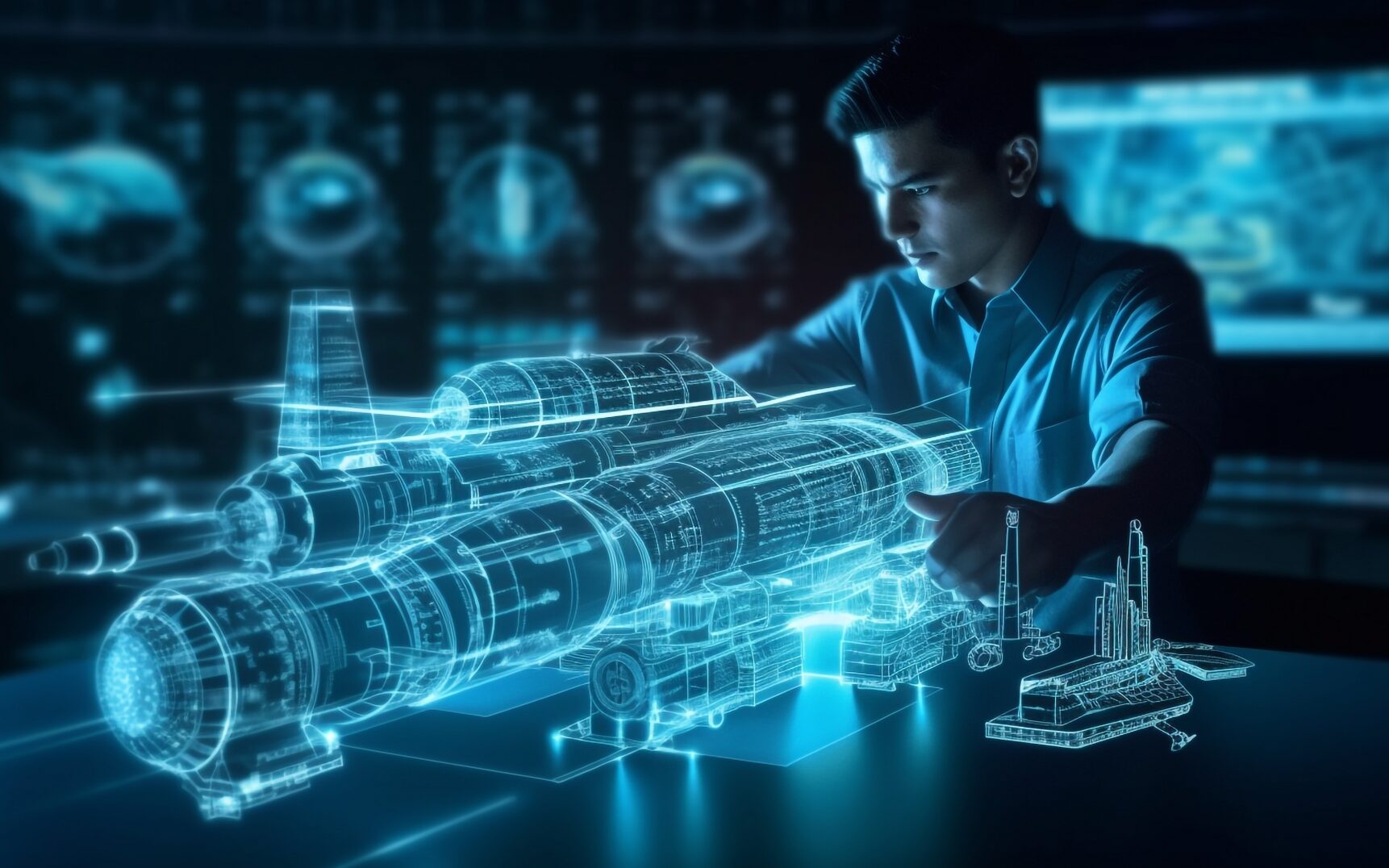
工場をスマートファクトリー化することによって、以下のような利点が期待できます。
- 生産性の向上につながる
- 人材の負担が減る
データ整理や活用が上手くできず、生産性が上がらない企業におすすめなのでご参考ください。
生産性の向上につながる
工場をスマートファクトリー化することによって、データ管理や分析で数字が見える化して無駄な部分が明確になります。
また、品質が数値化できるため、ロボットや機材の調整を定量的に行えるので生産性が大幅に上がります。
従来、なぜ生産性が上がらなかったのかという疑問がIT技術の導入で改善につながるでしょう。
人材の負担が減る
データ管理や整理を手で打ち込む場合、かなりの時間と労力が必要です。
機械に表示される数字を逐一メモをして、打ち込むことを繰り返す業務は従業員にとって楽ではありません。
機器から自動でパソコンあてにデータが送信され、送信されたデータをまとめるだけで済むので業務にかかる時間が大幅に減少します。
また、目で見て計算する方法よりも精度が向上するため、データの正確性が上がるメリットもあります。
自社での課題解決に詰まった時に経営コンサルタントを頼るメリット
製造業を営んでいくなかで、経営課題を抱えても対処法がわからず、苦しいまま経営を続けている方は経営コンサルタントへの相談をおすすめします。
経営コンサルタントを頼るメリットとしては、以下のようなことが挙げられるので詳しく解説します。
- 経営課題の抽出をしてもらえる
- 無駄な経費と会計ミスの是正をしてもらえる
- 工場別の課題をまとめ経営活性化を支援してもらえる
- 幹部・人材育成を代行してもらえる
- 運営体制の見直しと売り上げ向上に繋げてもらえる
前述にあった、マニュアルの作成やスマートファクトリー化などに悩んでいる場合、当社含めてコンサルタントに相談するのをおすすめします。
経営課題の抽出をしてもらえる
経営コンサルタントに依頼することによって、経営課題の抽出を依頼できます。
例えば、自社で資金繰りに悩んでいて、資金さえあれば何とかなると思っていたとします。
しかし、経営コンサルタントに相談したら仕入れの金額や会計のミスなど、細かい課題を発見してもらえます。
課題に感じていなくても、実は経営を揺るがす大きな原因である可能性があるので注意しなければいけません。
当社では、そんな経営課題を抽出して時に指摘し是正に向けて動かせていただいております。
無駄な経費と会計ミスの是正をしてもらえる
経営コンサルタントに依頼すると、無駄につかってしまっている販管費や接待交際費などの経費、会計ミスを是正して正しい方向に軌道修正をしてもらえます。
本来使わずに溜まっていたはずのお金が手元に残り、運転資金を確保できるので資金の不安を削減できます。
また、当社のように会計回りの一部を代行するコンサルタントの場合、実務に集中できるので安心して経営に集中できるでしょう。
会計をプロが確認するため、横領などが起こっていた場合にすぐに発見してもらえることもメリットです。
工場別の課題をまとめ経営活性化を支援してもらえる
複数の工場を保有している場合、管理が行き届かずA工場は良くてもC工場がトラブル続きということは少なくありません。
経営コンサルタントに依頼することによって、各工場の課題を把握し必要な人材の選定やトラブルシューティングに動いてもらえます。
経営者の手が届かない範囲も支援してもらえることから、管理業務を切り分けて一時的にまかせられることはメリットといえるでしょう。
幹部・人材育成を代行してもらえる
経営課題が積み重なっている場合、幹部や幹部候補への伝達の仕方がわからずに経営者一人で問題を抱えて解決に取り組むケースは少なくありません。
本来、経営課題は会社が一丸となって動かなければ解決しないため、動ける幹部が必要です。
動ける幹部がいない場合、経営コンサルタントに忙しい経営者に変わり幹部育成をしてもらいましょう。
複数社で様々なタイプの人材を見ているため、幹部に必要な知識を心得ているので、必要な力を最短距離で身に着けてもらえます。
運営体制の見直しと売り上げ向上に繋げてもらえる
経営課題の中で、会社の運営体制に課題がある場合に見直しを経営コンサルタントに依頼できます。
また、取引先への単価交渉や新規開拓の支援として、資料の是正などを依頼できます。
経営課題の解決に加えて、売上に直結する営業支援のような動きもしてもらえるので、大きなメリットとなるでしょう。
エスエスコンサルティングの製造業支援事例
製造業の経営課題についてお伝えしましたが、実際に企業はどのような課題を抱えてどのような施策を行うことで解決に繋がったのかを当社事例を紹介します。
菓子製造
課題
店舗ごとの売上は本部で把握していたが、人件費などその他の経費の管理は曖昧になっていた。また経営会議や売上計画もなく、「なんとなく」の状態で店舗運営が行われていた。
施策
・管理会計
各店舗の財務状況を一元確認できるよう、管理会計を導入した。店長が設定した売上計画に沿って運営ができるようにマネジメントを実施。
・経営会議
経営会議を毎月主催し、店舗ごとの月次目標の達成状況を経営陣が把握できるようにした。
結果
管理会計によって各店舗の経費を細かく把握できた。そのデータをもとに、月次目標の設定と達成するまでのサポートを実施したところ、平均売上120%を達成した。
荷役搬送機器設備の設計・製造・販売
課題
もともと設備の生産管理については仕組み化されていたが、その情報を十分に経営に活かしているとはいえなかった。 そんな状況下でコロナ禍となり、経営側のリーダーシップが求められるようになった。
施策
・管理会計
生産管理で得たデータをもとに製造原価を算出。そのデータをもとに販売価格を決定するなど、曖昧だった販売価格の基準を作った。
結果
管理会計導入の結果、経営者が生産と販売のデータを常に把握できるようになり、営業方針を先導しやすくなった。 コロナ禍においても売上の現状維持に成功。新規事業の立ち上げにリソースを振り分けることができるようになった。
鉄鋼製造業
課題
既存の商材の売上が減少傾向にあり、新規事業の立ち上げを行なったが、売上は改善せず債務超過に陥った。
状況を改善するために新規営業が必要だったが、営業のノウハウが足りていなかった。
施策
・営業戦略
幹部社員自らが営業活動を行うようにし、ノウハウの支援とKPI管理を行なった。
・管理会計
鍛鋼製品の製造原価のデータをもとに販売価格を決定。安易な値引きが起きないようにした。
結果
新規営業のKPI管理とPDCAによる改善の結果、1年で32社の新規取引先増加に成功し、4,000万円の売上アップを実現した。
経営課題に直面したら第三者に相談
在庫を抱える製造業において、経営課題を少しでも感じたら第三者への相談は早めに行いましょう。
取り引き先の銀行や仲間の経営者、経営コンサルタントなど頼れる相手は多いです。
取り返しのつかない局面になってしまった場合、手を差し伸べて貰うことは困難になるため悩み抜くまえに悩みの種をなくしておきましょう。
エスエスコンサルティングでは、複数社の製造業の支援実績があり各社それぞれの経営課題に取り組んでまいりました。
現在悩みを抱えている経営者の方は、まずは無料相談から受け付けておりますのでご相談ください。
事例集もあるため、自社の課題に少しでも似ていると思ったら、「こんなことできる?」と気軽にお尋ねくださいませ。